Innovations in Rubber Process Oil: Trends and Future Directions
Introduction to Rubber Process Oil
Rubber Process Oil is a vital ingredient in the production of various rubber products, including tires, footwear, automotive components, and industrial goods. It is used to enhance the processability of rubber, improve the flexibility of the finished products, and reduce the cost of manufacturing. The type and quality of RPO used can significantly affect the properties of rubber, such as elasticity, tensile strength, and resistance to aging.
Types of Rubber Process Oil
There are several types of Rubber Process Oils, each with its own characteristics and applications:
- Aromatic Rubber Process Oil: Known for its excellent solvency, this type is commonly used in the production of tires and industrial rubber products.
- Naphthenic Rubber Process Oil: This oil is valued for its low-temperature performance and stability, making it ideal for rubber products used in colder climates.
- Paraffinic Rubber Process Oil: With its high flash point and low volatility, paraffinic oil is used in applications where heat resistance is essential.
Recent Innovations in Rubber Process Oil
1. Development of Bio-based Rubber Process Oils
Benefits of Bio-based Rubber Process Oils:
- Sustainability: Derived from renewable resources, reducing the carbon footprint of rubber production.
- Improved Performance: Enhanced aging resistance and compatibility with a wide range of rubber compounds.
- Regulatory Compliance: Meets the growing demand for environmentally friendly products, particularly in regions with strict environmental regulations.
2. Advanced Additives for Enhanced Performance
Key Additives in Modern Rubber Process Oils:
- Antioxidants: Protect rubber products from oxidative degradation, extending their lifespan.
- Plasticizers: Improve the flexibility and processability of rubber, reducing energy consumption during manufacturing.
- Processing Aids: Enhance the flow properties of rubber compounds, leading to smoother production processes and higher quality finished products.
3. Tailored Formulations for Specific Applications
Examples of Tailored Formulations:
- High-Temperature Resistant RPOs: Designed for applications where rubber products are exposed to extreme heat, such as in automotive engines.
- Low-Temperature Resistant RPOs: Ideal for rubber products used in cold climates, ensuring flexibility and durability even at low temperatures.
- Eco-friendly RPOs: Formulated to minimize environmental impact, with reduced levels of harmful substances and improved biodegradability.
Trends Shaping the Future of Rubber Process Oil

The future of Rubber Process Oil is being shaped by several key trends that reflect the evolving needs of the rubber industry and the broader environmental landscape.
1. Sustainability and Eco-friendly Innovations
The Role of Regulatory Bodies:
- Stricter Regulations: Governments and regulatory bodies worldwide are imposing stricter limits on the use of hazardous substances in rubber products, pushing manufacturers to adopt safer and more sustainable RPOs.
- Green Certifications: The demand for rubber products with green certifications, such as those that meet the requirements of the EU REACH regulation, is on the rise.
2. Technological Advancements in RPO Production
Key Technological Innovations:
- Hydrotreating Technology: A refining process that removes impurities from RPO, resulting in oils with lower sulfur content and better oxidative stability.
- Catalytic Dewaxing: A process that improves the low-temperature properties of RPO, making it suitable for use in colder climates.
- Nano-additives: The incorporation of nano-sized additives in RPOs to enhance their performance, particularly in terms of wear resistance and thermal stability.
3. Demand for High-performance Rubber Products
High-performance Applications:
- Automotive Industry: The development of RPOs for high-performance tires, engine components, and seals that can withstand extreme conditions.
- Aerospace Industry: The need for RPOs that offer exceptional resistance to harsh environments, including high-altitude and high-speed conditions.
- Industrial Applications: The use of RPOs in industrial rubber products that require long-lasting performance and reliability.
Future Directions in Rubber Process Oil
1. Development of Next-generation Bio-based Oils
Potential Advantages:
- Higher Yield: Next-generation bio-based oils may offer higher yield and better performance than current bio-based options.
- Compatibility with Advanced Rubber Compounds: These oils are expected to be more compatible with advanced rubber compounds, enabling the production of high-performance, eco-friendly rubber products.
2. Integration of Smart Technologies
Smart Technologies in RPO:
- AI-driven Formulation: Using AI to predict the optimal combination of additives and base oils for specific applications, leading to more efficient and effective RPO formulations.
- Real-time Monitoring: The use of sensors to monitor the performance of RPO in real-time, allowing for adjustments during the production process to ensure consistent quality.
- Predictive Maintenance: Leveraging data analytics to predict when rubber products may fail due to RPO degradation, enabling timely maintenance and replacement.
3. Collaboration and Innovation in the Rubber Industry
Key Collaborative Efforts:
- Joint Research Initiatives: Collaborative research projects aimed at developing new RPO formulations and technologies.
- Industry Standards: The development of industry standards for RPO that promote sustainability and innovation.
- Knowledge Sharing: The exchange of knowledge and best practices between industry players to accelerate the adoption of new technologies and processes.
Final Thoughts
The Rubber Process Oil industry is undergoing a significant transformation, driven by the need for more sustainable, high-performance, and technologically advanced products. As the industry continues to evolve, innovations in RPO will play a critical role in shaping the future of rubber manufacturing. From bio-based oils to smart technologies and collaborative efforts, the future of Rubber Process Oil is set to be dynamic and exciting. These advancements not only promise to enhance the performance and sustainability of rubber products but also align with the broader global push towards environmental responsibility.
FAQs
Rubber Process Oil is made through the refining and processing of crude oil. The process involves several steps:
- Crude Oil Distillation: The crude oil is heated and separated into various fractions, with the heavier fractions being used to produce Rubber Process Oil.
- Hydrotreating: The heavy fractions undergo hydrotreating to remove impurities such as sulfur and nitrogen, which enhances the stability and performance of the oil.
- Blending: The treated oil is then blended with additives to achieve the desired properties, such as viscosity, solvency, and compatibility with rubber compounds.
Rubber Process Oils can be classified into three main types based on their chemical composition and properties:
- Aromatic Rubber Process Oil: Contains a high percentage of aromatic hydrocarbons, making it suitable for products like tires and industrial rubber goods.
- Naphthenic Rubber Process Oil: Known for its low-temperature performance and stability, often used in rubber products for colder climates.
- Paraffinic Rubber Process Oil: Characterized by a high flash point and low volatility, making it ideal for heat-resistant rubber products.
The viscosity of Rubber Process Oil varies depending on the type of oil and its specific formulation. Generally, RPOs have a viscosity range of 100 to 500 centistokes (cSt) at 40°C. The viscosity is crucial as it affects the processability of the rubber compound and the performance of the final product.
Rubber Process Oils are oils used as processing aids in the rubber industry. They are added to rubber compounds to improve the processability, enhance the flexibility and durability of the finished products, and reduce manufacturing costs. RPOs are essential in the production of tires, automotive components, footwear, and various industrial rubber goods.

Does Your Car Need High Mileage Oil? (Signs You Should Switch)
Does Your Car Need High Mileage Oil? (Signs You Should Switch) Discover More As vehicles age, their engines undergo significant wear, leading to reduced efficiency and potential breakdowns. One of the most effective ways to maintain an older engine is by switching to high-mileage oil, specially formulated for cars with 75,000 miles or more. But how do you know if your car needs it? What are the key benefits, drawbacks, and alternatives? And why should you consider Ruamnza Xrace Pro Oil for your high-mileage vehicle?

Does Your Diesel Engine Need a Special Oil? (The Truth Revealed)
Does Your Diesel Engine Need a Special Oil? (The Truth Revealed) Discover More When it comes to maintaining a diesel engine, one of the most critical decisions you’ll make is choosing the right oil. Diesel engines operate under extreme conditions—high compression, intense heat, and heavy loads—which means they require a lubricant that can withstand these challenges. But does your diesel engine really need a special oil, or can you use any high-quality motor oil? In this comprehensive guide, we’ll uncover the

What is Anti-Freeze Coolant? Types, Colors & How to Use
What is Anti-Freeze Coolant? Types, Colors & How to Use Discover More Anti-freeze coolant, also known as engine coolant or radiator fluid, is a specially formulated liquid that regulates engine temperature, prevents overheating in summer, and protects against freezing in winter. It is a mixture of water, ethylene glycol or propylene glycol, and chemical additives that enhance engine efficiency and longevity. Without proper coolant, engines can suffer from: Overheating (leading to warped cylinder heads or blown gaskets) Freezing (causing cracked engine blocks in cold climates) Corrosion (damaging radiators,
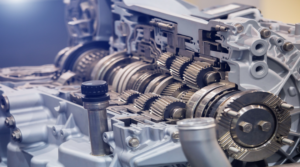
What is ATF? Types of Transmission Fluid & When to Change It
What is ATF? Types of Transmission Fluid & When to Change It Discover More Transmission fluid is one of the most critical yet often overlooked components in a vehicle’s maintenance routine. Whether you drive an automatic, manual, continuously variable transmission (CVT), or dual-clutch transmission (DCT) vehicle, the right transmission fluid ensures smooth operation, longevity, and peak performance. What is Automatic Transmission Fluid (ATF)? Automatic Transmission Fluid (ATF) is a specialized lubricant designed to reduce friction, cool transmission components, and facilitate smooth
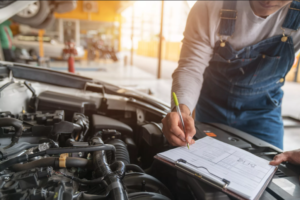
Fuel Injector Cleaner: Does It Really Work? (Analysis, Benefits, and Top Picks)
Fuel Injector Cleaner: Does It Really Work? (In-Depth Analysis, Benefits, and Top Picks) Discover More Modern engines rely on precise fuel delivery to maintain performance, efficiency, and emissions compliance. Fuel injectors play a critical role in this process by atomizing fuel into a fine mist for optimal combustion. However, over time, carbon deposits, varnish, and contaminants can clog injectors, leading to poor engine performance. Fuel injector cleaners are chemical additives designed to dissolve these deposits and restore injector efficiency. But do they
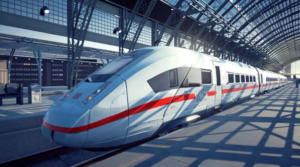
Best Railroad Engine Oils in 2025 – Boost Performance & Longevity
Best Railroad Engine Oils in 2025 – Boost Performance & Longevity Discover More The railroad industry is a backbone of global logistics, transporting millions of tons of cargo and passengers daily. Given the immense stress on locomotive engines, selecting the best railroad engine oil is crucial for optimal performance, fuel efficiency, and engine longevity. In 2025, advancements in lubrication technology have led to high-performance synthetic blends, low-ash formulations, and smart additives that enhance engine protection under extreme conditions. This guide
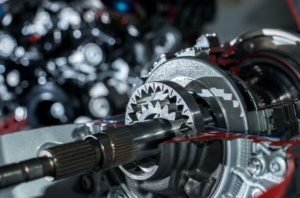
Best Transmission Treatments to Extend Your Vehicle’s Lifespan (2025 Guide)
Best Transmission Treatments to Extend Your Vehicle’s Lifespan Discover More Maintaining your vehicle’s transmission is crucial for ensuring longevity, smooth performance, and fuel efficiency. With advancements in automotive technology, transmission treatments have evolved significantly in 2025. This guide explores the best transmission treatments available, their benefits, and how they can help extend your vehicle’s lifespan. Understanding Transmission Systems and Their Importance A vehicle’s transmission is responsible for transferring power from the engine to the wheels, enabling smooth gear shifts and