Antiwear Additives: Types, Mechanisms, Role and App
In industrial machinery and automotive applications, wear and friction are unavoidable but damaging effects on metal parts. Over time, they lead to reduced efficiency, increased maintenance costs, and eventually the failure of critical components. Antiwear additives are chemical compounds that play a crucial role in mitigating these effects. By forming protective layers on metal surfaces, they reduce the rate of wear and extend the lifespan of machinery. In this article, we’ll dive into the various types, mechanisms, and applications of antiwear additives, as well as explore the latest innovations shaping their future.
Role of Antiwear Additives in Modern Lubricants
Modern lubricants are designed not only to reduce friction but also to minimize wear on moving parts. Antiwear additives enhance the performance of these lubricants by providing an extra layer of protection under high-pressure conditions, preventing metal-to-metal contact that leads to wear. Through chemical and physical mechanisms, they improve the load-bearing capacity of lubricants, ensuring that machinery operates smoothly even under demanding conditions. The role of antiwear additives is thus central to achieving efficient, long-lasting machinery performance.
Why Equipment Needs Protection Against Premature Wear
Premature wear on machinery parts can lead to a cascade of operational problems, ranging from decreased productivity to costly repairs and replacement of parts. Friction between moving parts generates heat, leading to material degradation over time. In the absence of adequate protection, metal surfaces in engines, transmissions, and hydraulic systems suffer from wear that compromises functionality. Antiwear additives help by reducing the amount of direct metal contact, enabling smoother operation and prolonging equipment life.
Types of Antiwear Additives

Several types of antiwear additives are commonly used, each tailored to specific applications. These additives are selected based on factors such as operating conditions, desired performance characteristics, and environmental considerations. The most prominent types are:
-
Zinc Dialkyldithiophosphates (ZDDP): One of the most widely used antiwear additives, ZDDP provides excellent protection in high-pressure environments. When exposed to high temperatures and pressures, ZDDP decomposes and forms a protective phosphate film on metal surfaces, effectively reducing wear.
-
Phosphorus-Based Additives: Phosphorus-based additives are highly effective in applications involving extreme pressures. They create durable phosphate layers that protect metal surfaces from wear and prevent oxidation.
-
Sulfur-Based Additives: Typically used in combination with phosphorus, sulfur-based additives provide enhanced protection in high-load conditions. Sulfur compounds react with metal surfaces to form protective films, particularly useful in applications involving heavy machinery.
-
Ashless Additives: Designed for applications with strict environmental standards, ashless additives avoid leaving residue or “ash” when burned, making them suitable for eco-friendly applications. These additives offer effective wear protection without contributing to pollutant emissions.
In addition to these standard types, custom formulations are being developed to cater to specific industrial needs, reflecting ongoing innovation in antiwear technology.
How Antiwear Additives Work: Mechanisms of Action
Antiwear additives operate through a combination of chemical and physical mechanisms that create protective barriers on metal surfaces. Two key mechanisms that illustrate how they function are:
Surface Reaction: Under high pressure and heat, antiwear additives chemically react with metal surfaces, forming protective compounds like metal phosphates or sulfides. These compounds create a thin film that shields the metal surface from direct contact, reducing wear and friction.
Tribofilm Formation: Tribofilms are self-generating films that form on metal surfaces during frictional contact. As friction generates heat, antiwear additives decompose and adhere to the metal surfaces, creating a stable, low-friction layer. This tribofilm plays a significant role in preserving surface integrity during operation.
These mechanisms enable antiwear additives to maintain the longevity of metal components, particularly in harsh environments where friction and wear are constant threats.
Applications Across Industries: Where Antiwear Additives Excel
Antiwear additives are indispensable across various industries that rely on machinery and equipment for daily operations. They are tailored to specific applications to provide optimal performance and protection. Some of the key industries that utilize antiwear additives include:
Automotive Applications: In engines, transmissions, and other automotive systems, antiwear additives help protect components from the extreme conditions of internal combustion and high-speed operation. ZDDP and similar additives are common in automotive lubricants to prevent wear on engine parts.
Industrial Machinery: Heavy equipment used in construction, mining, and manufacturing industries is exposed to heavy loads and high stress. Antiwear additives are essential in hydraulic fluids and gear oils used in these applications, reducing maintenance costs and preventing premature equipment failure.
Aerospace: Antiwear additives are used in the aerospace industry to protect critical components such as turbine engines and hydraulic systems. Given the extreme temperatures and pressures in aerospace applications, high-performance additives are formulated to withstand these unique demands.
Marine Equipment: Marine machinery operates in highly corrosive environments, requiring lubricants with both antiwear and anticorrosion properties. Specialized antiwear additives help protect marine engines, propeller shafts, and gear systems from wear caused by both friction and corrosion.
Each of these applications benefits significantly from antiwear additives, which ensure machinery reliability and longevity across diverse operating conditions.
Benefits of Antiwear Additives in Equipment Maintenance
Antiwear additives provide numerous benefits that make them a staple in equipment maintenance strategies. Some of the main advantages include:
Extended Equipment Lifespan: By reducing wear on moving parts, antiwear additives contribute to a longer operational life for machinery and reduce the frequency of part replacements.
Reduced Maintenance Costs: Equipment maintenance can be costly, especially for industrial machinery. Antiwear additives decrease the need for frequent repairs and part replacements, resulting in significant cost savings.
Enhanced Performance: By minimizing friction, antiwear additives help machinery operate smoothly, improving overall efficiency and reducing energy consumption.
Lower Environmental Impact: Some antiwear additives, especially ashless ones, are designed to be more environmentally friendly. By reducing the rate of component wear, they also lower the need for replacements, thus reducing waste.
Environmental and Regulatory Considerations
While antiwear additives are highly beneficial, there are environmental and regulatory considerations to take into account. Some traditional additives, like ZDDP, release elements such as zinc and phosphorus into the environment, which can contribute to pollution. To address these concerns, regulatory bodies have imposed limits on the use of certain additives in specific applications, particularly in automotive and industrial sectors. In response, manufacturers are developing eco-friendly alternatives, such as ashless additives, that provide wear protection without leaving harmful residues. The industry continues to adapt to these evolving regulations, balancing the need for effective wear protection with environmental responsibility.
Future of Antiwear Additives: Innovations and Emerging Trends
The future of antiwear additives is marked by exciting innovations and trends. Two areas gaining significant attention are:
Eco-Friendly Formulations: Environmental concerns are driving the development of additives that are less harmful to ecosystems. Research is focused on creating biodegradable and ashless antiwear additives that provide the same level of protection without the environmental drawbacks.
Nano-Additives: Nanotechnology is being explored as a means to enhance wear protection at a molecular level. Nano-additives consist of nanoparticles that can create a stronger, more resilient protective film, offering even greater protection against wear.
Hybrid Additives: These combine the benefits of multiple types of additives to address complex operational conditions. Hybrid formulations are especially promising in industries with extreme requirements, such as aerospace and heavy manufacturing.
These innovations represent the next generation of antiwear additives, promising better performance, reduced environmental impact, and enhanced adaptability across different applications.
Conclusion: The Importance of Antiwear Additives in Modern Industry
Antiwear additives are essential components in modern lubricants, ensuring that machinery and equipment function efficiently and remain protected under strenuous conditions. From automotive engines to heavy-duty industrial machinery, these additives play a critical role in preventing premature wear and maintaining performance. The innovations on the horizon, including eco-friendly and nano-enhanced additives, will further strengthen their impact, balancing performance with environmental considerations. As technology and industry demands evolve, antiwear additives will continue to be a cornerstone of equipment maintenance, prolonging the life of machinery and reducing operational costs across numerous sectors.
FAQs

Does Your Car Need High Mileage Oil? (Signs You Should Switch)
Does Your Car Need High Mileage Oil? (Signs You Should Switch) Discover More As vehicles age, their engines undergo significant wear, leading to reduced efficiency and potential breakdowns. One of the most effective ways to maintain an older engine is by switching to high-mileage oil, specially formulated for cars with 75,000 miles or more. But how do you know if your car needs it? What are the key benefits, drawbacks, and alternatives? And why should you consider Ruamnza Xrace Pro Oil for your high-mileage vehicle?

Does Your Diesel Engine Need a Special Oil? (The Truth Revealed)
Does Your Diesel Engine Need a Special Oil? (The Truth Revealed) Discover More When it comes to maintaining a diesel engine, one of the most critical decisions you’ll make is choosing the right oil. Diesel engines operate under extreme conditions—high compression, intense heat, and heavy loads—which means they require a lubricant that can withstand these challenges. But does your diesel engine really need a special oil, or can you use any high-quality motor oil? In this comprehensive guide, we’ll uncover the

What is Anti-Freeze Coolant? Types, Colors & How to Use
What is Anti-Freeze Coolant? Types, Colors & How to Use Discover More Anti-freeze coolant, also known as engine coolant or radiator fluid, is a specially formulated liquid that regulates engine temperature, prevents overheating in summer, and protects against freezing in winter. It is a mixture of water, ethylene glycol or propylene glycol, and chemical additives that enhance engine efficiency and longevity. Without proper coolant, engines can suffer from: Overheating (leading to warped cylinder heads or blown gaskets) Freezing (causing cracked engine blocks in cold climates) Corrosion (damaging radiators,
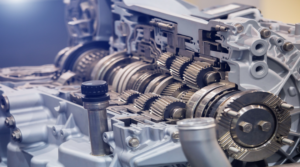
What is ATF? Types of Transmission Fluid & When to Change It
What is ATF? Types of Transmission Fluid & When to Change It Discover More Transmission fluid is one of the most critical yet often overlooked components in a vehicle’s maintenance routine. Whether you drive an automatic, manual, continuously variable transmission (CVT), or dual-clutch transmission (DCT) vehicle, the right transmission fluid ensures smooth operation, longevity, and peak performance. What is Automatic Transmission Fluid (ATF)? Automatic Transmission Fluid (ATF) is a specialized lubricant designed to reduce friction, cool transmission components, and facilitate smooth
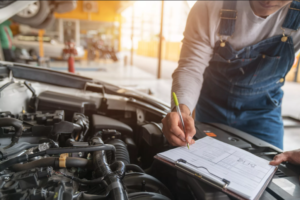
Fuel Injector Cleaner: Does It Really Work? (Analysis, Benefits, and Top Picks)
Fuel Injector Cleaner: Does It Really Work? (In-Depth Analysis, Benefits, and Top Picks) Discover More Modern engines rely on precise fuel delivery to maintain performance, efficiency, and emissions compliance. Fuel injectors play a critical role in this process by atomizing fuel into a fine mist for optimal combustion. However, over time, carbon deposits, varnish, and contaminants can clog injectors, leading to poor engine performance. Fuel injector cleaners are chemical additives designed to dissolve these deposits and restore injector efficiency. But do they