Mixed Hydrocarbon Oil Specifications: A Comprehensive Guide
Mixed Hydrocarbon Oils
Mixed hydrocarbon oils are complex blends of hydrocarbons, primarily consisting of paraffins, naphthenes, and aromatics. These oils are versatile and used across various industries due to their adaptability and effectiveness in different operating conditions. They serve as base oils in lubricants, hydraulic fluids, and other industrial products, ensuring smooth operation and protection against wear and tear.
Key Specifications of Mixed Hydrocarbon Oils
The performance and suitability of mixed hydrocarbon oils depend largely on their specifications. These specifications are determined by several factors, including the composition, viscosity, flash point, pour point, and purity. Understanding these specifications is essential for selecting the right oil for your specific application.
Viscosity
- Definition and Importance: Viscosity refers to the oil’s resistance to flow. It is a critical parameter as it influences the lubrication properties of the oil. Higher viscosity oils provide better lubrication but may result in increased resistance and energy consumption, whereas lower viscosity oils ensure smoother flow but may not offer adequate lubrication under high-pressure conditions.
- Measurement: Viscosity is measured in centistokes (cSt) at specific temperatures, typically 40°C and 100°C. The choice of viscosity grade depends on the operating temperature and the load conditions of the equipment.
Flash Point
- Definition and Importance: The flash point of mixed hydrocarbon oil is the temperature at which it emits enough vapor to ignite in air. This specification is crucial for safety, especially in applications involving high temperatures or potential exposure to open flames.
- Standards: The flash point is typically measured in degrees Celsius (°C) and must meet industry standards to ensure safe operation. Oils with higher flash points are preferred for high-temperature applications.
Pour Point
- Definition and Importance: The pour point is the lowest temperature at which the oil remains fluid and can be poured. It indicates the oil’s ability to function in cold environments. For applications in colder climates, selecting a mixed hydrocarbon oil with a low pour point is essential to prevent freezing or solidification.
- Relevance: Understanding the pour point helps in choosing the right oil for environments with varying temperatures, ensuring that the machinery operates smoothly regardless of external conditions.
Sulfur Content
- Definition and Importance: Sulfur content in mixed hydrocarbon oils is a critical specification, especially for environmental and performance reasons. High sulfur content can lead to increased emissions and corrosion within the machinery.
- “Low sulfur content” or “reduced sulfur levels” are important considerations for industries aiming to minimize environmental impact and enhance the longevity of their equipment.
Purity
- Definition and Importance: The purity of mixed hydrocarbon oil is defined by the absence of impurities such as water, sediments, and other contaminants. High-purity oils ensure better performance and reduce the risk of damage to the equipment.
- Standards: Purity is often ensured through rigorous refining processes and adherence to industry standards. Oils with higher purity levels are preferred for critical applications where even minor impurities can cause significant issues.
Applications of Mixed Hydrocarbon Oils

The versatility of mixed hydrocarbon oils makes them suitable for a wide range of applications across various industries. Understanding the specifications helps in determining the most appropriate oil for each specific use.
Automotive Industry
- Engine Oils: Mixed hydrocarbon oils are used as base oils in engine lubricants, providing the necessary viscosity and lubrication properties required for internal combustion engines. Their ability to maintain performance under high temperatures and pressures makes them ideal for automotive applications.
- Transmission Fluids: The specifications of mixed hydrocarbon oils, particularly their viscosity and purity, make them suitable for use in transmission fluids, ensuring smooth gear shifts and reducing wear on transmission components.
Marine Industry
- Marine Lubricants: In the marine industry, mixed hydrocarbon oils are used in lubricants for ship engines and other equipment. The oils’ flash point and sulfur content are particularly important in this sector, as they must meet stringent safety and environmental regulations.
- Hydraulic Fluids: Mixed hydrocarbon oils are also used in hydraulic systems on ships, where their stability and low pour point ensure reliable operation in varying temperature conditions.
Industrial Applications
- Machinery Lubricants: Industrial machinery, such as compressors, turbines, and pumps, rely on mixed hydrocarbon oils for lubrication. The viscosity and purity of the oil play crucial roles in preventing wear and tear and ensuring efficient operation.
- Heat Transfer Fluids: In applications where heat transfer is critical, mixed hydrocarbon oils are used due to their high thermal stability and appropriate viscosity. They ensure efficient heat transfer while maintaining their integrity under high temperatures.
Environmental and Regulatory Considerations
As industries move towards more sustainable practices, the specifications of mixed hydrocarbon oils, particularly in terms of sulfur content and environmental impact, have come under greater scrutiny. Meeting environmental regulations is not only a legal requirement but also a step towards corporate responsibility.
Low Sulfur Content
- Importance: The shift towards low sulfur content in mixed hydrocarbon oils is driven by the need to reduce emissions and meet environmental regulations. Oils with low sulfur content produce fewer pollutants and are less corrosive, extending the lifespan of equipment.
- Compliance: Industries are required to adhere to environmental regulations that limit sulfur content in oils. Compliance with these regulations ensures not only legal operation but also contributes to the global effort to reduce air pollution.
Biodegradability
- Importance: Biodegradability is another critical specification for mixed hydrocarbon oils, especially in applications where accidental spills could occur. Biodegradable oils minimize environmental damage and are increasingly preferred in environmentally sensitive industries.
- Standards: Biodegradable mixed hydrocarbon oils must meet specific industry standards to be considered environmentally friendly. These standards often involve rigorous testing to ensure the oil breaks down effectively without harming the ecosystem.
Recycling and Re-refining
- Importance: The re-refining of mixed hydrocarbon oils is an essential practice in promoting sustainability. Re-refining involves processing used oil to remove impurities and restore its original specifications, reducing the demand for virgin oil production and minimizing waste.
- Impact: By focusing on recycling and re-refining, industries can reduce their environmental footprint, conserve resources, and comply with waste management regulations.
Choosing the Right Mixed Hydrocarbon Oil
Selecting the appropriate mixed hydrocarbon oil for your application involves understanding the specific requirements of your machinery and the operating conditions. The following factors should be considered:
Operating Temperature
- Consideration: The temperature at which your machinery operates will significantly influence the choice of mixed hydrocarbon oil. Oils with the appropriate viscosity and pour point should be selected to ensure optimal performance across the temperature range.
Load and Pressure
- Consideration: The load and pressure conditions of your machinery determine the required viscosity and lubrication properties of the oil. For high-load conditions, oils with higher viscosity may be necessary to provide adequate protection and reduce wear.
Environmental Regulations
- Consideration: Ensure that the selected oil meets all relevant environmental regulations, particularly in terms of sulfur content and biodegradability. This is especially important for industries operating in regions with strict environmental laws.
Equipment Manufacturer Recommendations
- Consideration: Always refer to the equipment manufacturer’s recommendations when selecting mixed hydrocarbon oil. These recommendations are based on extensive testing and are tailored to the specific needs of your machinery.
Cost vs. Performance
- Consideration: While cost is always a factor, it should not be the sole determinant in selecting mixed hydrocarbon oil. The performance and longevity of the oil, along with its ability to protect your machinery, should weigh heavily in the decision-making process.
Final Thoughts
Understanding the specifications of mixed hydrocarbon oils is crucial for optimizing the performance and lifespan of your machinery. From viscosity and flash point to sulfur content and biodegradability, each specification plays a role in determining the oil’s suitability for a particular application.
By selecting the right mixed hydrocarbon oil, industries can ensure efficient operation, comply with environmental regulations, and ultimately protect their investments. As technology advances and environmental standards become more stringent, staying informed about the latest developments in mixed hydrocarbon oil specifications will be essential for any industry professional.
In summary, mixed hydrocarbon oils are more than just lubricants; they are vital components that keep industries running smoothly. By focusing on the key specifications and understanding the importance of LSi keywords like “low sulfur content,” you can make informed decisions that benefit both your operations and the environment.
FAQs

Does Your Car Need High Mileage Oil? (Signs You Should Switch)
Does Your Car Need High Mileage Oil? (Signs You Should Switch) Discover More As vehicles age, their engines undergo significant wear, leading to reduced efficiency and potential breakdowns. One of the most effective ways to maintain an older engine is by switching to high-mileage oil, specially formulated for cars with 75,000 miles or more. But how do you know if your car needs it? What are the key benefits, drawbacks, and alternatives? And why should you consider Ruamnza Xrace Pro Oil for your high-mileage vehicle?

Does Your Diesel Engine Need a Special Oil? (The Truth Revealed)
Does Your Diesel Engine Need a Special Oil? (The Truth Revealed) Discover More When it comes to maintaining a diesel engine, one of the most critical decisions you’ll make is choosing the right oil. Diesel engines operate under extreme conditions—high compression, intense heat, and heavy loads—which means they require a lubricant that can withstand these challenges. But does your diesel engine really need a special oil, or can you use any high-quality motor oil? In this comprehensive guide, we’ll uncover the

What is Anti-Freeze Coolant? Types, Colors & How to Use
What is Anti-Freeze Coolant? Types, Colors & How to Use Discover More Anti-freeze coolant, also known as engine coolant or radiator fluid, is a specially formulated liquid that regulates engine temperature, prevents overheating in summer, and protects against freezing in winter. It is a mixture of water, ethylene glycol or propylene glycol, and chemical additives that enhance engine efficiency and longevity. Without proper coolant, engines can suffer from: Overheating (leading to warped cylinder heads or blown gaskets) Freezing (causing cracked engine blocks in cold climates) Corrosion (damaging radiators,
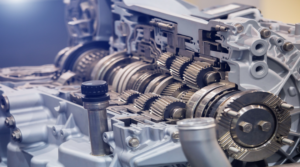
What is ATF? Types of Transmission Fluid & When to Change It
What is ATF? Types of Transmission Fluid & When to Change It Discover More Transmission fluid is one of the most critical yet often overlooked components in a vehicle’s maintenance routine. Whether you drive an automatic, manual, continuously variable transmission (CVT), or dual-clutch transmission (DCT) vehicle, the right transmission fluid ensures smooth operation, longevity, and peak performance. What is Automatic Transmission Fluid (ATF)? Automatic Transmission Fluid (ATF) is a specialized lubricant designed to reduce friction, cool transmission components, and facilitate smooth
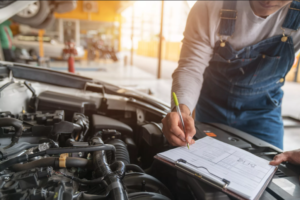
Fuel Injector Cleaner: Does It Really Work? (Analysis, Benefits, and Top Picks)
Fuel Injector Cleaner: Does It Really Work? (In-Depth Analysis, Benefits, and Top Picks) Discover More Modern engines rely on precise fuel delivery to maintain performance, efficiency, and emissions compliance. Fuel injectors play a critical role in this process by atomizing fuel into a fine mist for optimal combustion. However, over time, carbon deposits, varnish, and contaminants can clog injectors, leading to poor engine performance. Fuel injector cleaners are chemical additives designed to dissolve these deposits and restore injector efficiency. But do they
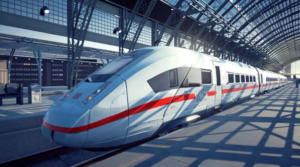
Best Railroad Engine Oils in 2025 – Boost Performance & Longevity
Best Railroad Engine Oils in 2025 – Boost Performance & Longevity Discover More The railroad industry is a backbone of global logistics, transporting millions of tons of cargo and passengers daily. Given the immense stress on locomotive engines, selecting the best railroad engine oil is crucial for optimal performance, fuel efficiency, and engine longevity. In 2025, advancements in lubrication technology have led to high-performance synthetic blends, low-ash formulations, and smart additives that enhance engine protection under extreme conditions. This guide
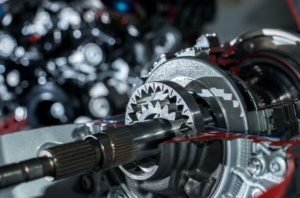
Best Transmission Treatments to Extend Your Vehicle’s Lifespan (2025 Guide)
Best Transmission Treatments to Extend Your Vehicle’s Lifespan Discover More Maintaining your vehicle’s transmission is crucial for ensuring longevity, smooth performance, and fuel efficiency. With advancements in automotive technology, transmission treatments have evolved significantly in 2025. This guide explores the best transmission treatments available, their benefits, and how they can help extend your vehicle’s lifespan. Understanding Transmission Systems and Their Importance A vehicle’s transmission is responsible for transferring power from the engine to the wheels, enabling smooth gear shifts and