Pour Point Depressants: Enhancing Lubricant Performance
What Are Pour Point Depressants?
Pour Point Depressants (PPDs) are specialized chemical additives used in lubricating oils, fuels, and various industrial fluids to lower their pour point—the lowest temperature at which the fluid remains pourable. As temperatures drop, waxes present in oils start to crystallize and solidify, leading to increased viscosity and potential gelling. This solidification can prevent the oil from flowing, posing a significant risk to the equipment and machinery relying on the lubricant for smooth operation.
PPDs work by inhibiting the formation and growth of these wax crystals, thereby maintaining the fluidity of the oil even in extremely cold conditions. This capability is essential in industries that operate in harsh environments, such as the automotive, marine, and aviation sectors, where machinery must perform reliably regardless of temperature fluctuations.
2. How Do Pour Point Depressants Work?
Crystal Modification Process
Pour point depressants modify the wax crystals by attaching to their surfaces as they form. By doing so, PPDs prevent the crystals from growing large enough to interact with each other and form a solid mass. Instead, the wax remains in a dispersed, fine state, which does not significantly affect the oil’s viscosity. This action is crucial in maintaining the fluidity of the oil and ensuring that it can continue to lubricate moving parts effectively, even in freezing temperatures.
Viscosity Control and Temperature Stability
The presence of PPDs also helps control the viscosity of the oil, which is a measure of its resistance to flow. By preventing the formation of large wax crystals, PPDs maintain the oil’s viscosity within a desirable range, allowing it to flow freely and reach critical components that need lubrication. This is particularly important for ensuring the smooth operation of engines and machinery in cold weather conditions.
3. Applications of Pour Point Depressants
Pour point depressants find application across a wide range of industries, each with specific requirements that necessitate the use of these additives. Below are some of the primary industries where PPDs are indispensable:
a) Automotive Industry
In the automotive industry, the performance and longevity of engines, transmissions, and gear systems heavily depend on the quality of lubricants used. Vehicles often operate in diverse temperature conditions, ranging from the extreme heat of summer to the sub-zero temperatures of winter. Pour point depressants are critical in engine oils, transmission fluids, and gear oils, ensuring that these lubricants remain fluid and effective, even in freezing conditions.
Cold starts can be particularly challenging for engines, as the oil tends to thicken when temperatures drop. PPDs help maintain the oil’s viscosity, ensuring it can circulate quickly upon startup, providing immediate protection to engine components.
b) Marine Industry
The marine industry, with its exposure to cold and harsh environments, also relies heavily on pour point depressants. Ships and other marine vessels often navigate through polar regions where temperatures can plummet to extreme lows. In such conditions, the lubricants used in engines, gear systems, and other critical machinery must remain fluid to prevent mechanical failures.
PPDs in marine oils prevent the solidification of wax, ensuring that the oil flows smoothly through the machinery, reducing wear and tear, and enhancing the longevity of the equipment.
c) Aviation Industry
Aircraft operate at altitudes where temperatures can drop drastically, especially during long-haul flights. The aviation industry requires lubricants that can perform reliably in these extreme conditions. Pour point depressants are used in aviation lubricants and hydraulic fluids to maintain fluidity at low temperatures, ensuring the safety and efficiency of flight operations.
The ability of PPDs to keep fluids operational in cold conditions is crucial for the proper functioning of hydraulic systems, landing gears, and other essential components of an aircraft.
d) Industrial Machinery
In industrial settings, especially in outdoor or cold-weather operations, pour point depressants play a vital role. Heavy machinery used in construction, mining, and other industries often operates in environments where temperatures can drop significantly. In such cases, PPDs in lubricants ensure that the machinery operates smoothly without the risk of oil gelling or solidification.
PPDs also help reduce the energy required to start machines in cold conditions, leading to increased operational efficiency and reduced wear on components.
4. Types of Pour Point Depressants

Several types of pour point depressants are available, each with unique properties suited to different applications and types of oils. The most commonly used PPDs include:
a) Polymethacrylates (PMAs)
Polymethacrylates are versatile and widely used pour point depressants, particularly in automotive lubricants. They are effective in a broad range of temperatures and are known for their ability to reduce the pour point of oils significantly. PMAs work by co-crystallizing with wax molecules, preventing them from growing large enough to hinder the oil’s flow.
b) Styrene Esters
Styrene esters are commonly used in industrial and gear oils. These PPDs are particularly effective in reducing pour points in oils with high paraffin content, where wax crystallization is a significant concern. Styrene esters offer excellent low-temperature performance and are often preferred in applications where thermal stability is critical.
c) Alkylated Naphthalene
Alkylated naphthalene pour point depressants are used in specialized lubricants, particularly in the aviation and aerospace industries, where a high degree of temperature stability is required. These PPDs offer exceptional low-temperature flow properties and are suitable for use in extreme conditions.
d) Olefins Copolymers
Olefins copolymers are highly effective in controlling the formation of wax crystals. They are widely used in both fuels and lubricants, providing excellent pour point depression and viscosity improvement. These PPDs are particularly useful in applications where both low-temperature performance and high-temperature stability are required.
5. Industry Trends and Innovations
As the demand for high-performance lubricants and fuels grows, the pour point depressant market is experiencing significant innovation. Several key trends and developments are shaping the future of PPDs:
a) Eco-Friendly Additives
With the global shift towards sustainability, there is an increasing focus on developing environmentally friendly pour point depressants. These additives are designed to be biodegradable, non-toxic, and have minimal environmental impact. The move towards greener PPDs aligns with stricter environmental regulations and the growing demand for sustainable products in various industries.
b) Nano-Technology Integration
Nanotechnology is being integrated into pour point depressants to enhance their efficiency. Nano-sized additives can interact with wax crystals at a more precise level, leading to better performance at lower dosages. This technology not only improves the effectiveness of PPDs but also reduces the overall cost of using these additives.
c) Customized Solutions
The lubricant and oil industries are increasingly demanding customized solutions tailored to specific applications. Manufacturers are responding by offering pour point depressants that are optimized for particular types of oils and operating conditions. This trend towards customization ensures that the PPDs used are perfectly suited to the unique requirements of the end-user, resulting in better overall performance.
6. Challenges in Using Pour Point Depressants
Despite their numerous benefits, the use of pour point depressants also comes with certain challenges. These challenges need to be carefully managed to ensure the optimal performance of the additives:
a) Compatibility Issues
Not all pour point depressants are compatible with every type of oil. Incompatibility can lead to reduced effectiveness or even adverse reactions, such as sludge formation or loss of fluid properties. It is crucial to select the right PPD for the specific oil type and application to avoid these issues.
b) Cost Considerations
High-quality pour point depressants can be expensive, and their cost-effectiveness needs to be evaluated in the context of the specific application and operating conditions. While PPDs can provide significant benefits, their use must be justified by the value they add in terms of improved performance and protection.
c) Regulatory Compliance
As environmental regulations become stricter, manufacturers must ensure that their pour point depressants comply with the latest standards. This is particularly important concerning the biodegradability and toxicity of the additives. Non-compliance can lead to penalties and restricted market access, making it essential for manufacturers to stay updated with regulatory changes.
7. The Future of Pour Point Depressants
The future of pour point depressants is poised for continued innovation and growth. As industries demand higher performance and greater sustainability, PPDs will evolve to meet these challenges. Key areas of development include:
a) Bio-Based Pour Point Depressants
One of the most promising developments is the creation of bio-based pour point depressants. These additives are derived from renewable sources, making them more environmentally friendly. As sustainability becomes a key focus across industries, the demand for bio-based PPDs is expected to grow.
b) Molecular Engineering
Advances in molecular engineering are allowing for the development of pour point depressants that are tailored at the molecular level for specific applications. This approach enables the creation of highly efficient PPDs that offer superior performance with minimal environmental impact.
c) Enhanced Performance
Research is ongoing to improve the effectiveness of pour point depressants, with a focus on increasing their efficiency while reducing the required dosage. This will make PPDs more cost-effective and allow for their use in a broader range of applications.
Final Thoughts
Pour point depressants are a vital component of modern lubrication and fuel technologies. Their ability to maintain fluidity in cold conditions ensures the reliable operation of machinery across various industries, from automotive and marine to aviation and industrial applications. As technology advances, PPDs will continue to evolve, offering even greater performance and sustainability.
The future of pour point depressants looks promising, with innovations such as bio-based additives, nanotechnology, and customized solutions leading the way. By addressing the challenges associated with their use and embracing the latest trends, the industry can look forward to a new era of efficient, eco-friendly pour point depressants that meet the demands of an increasingly complex world.
FAQs

Does Your Car Need High Mileage Oil? (Signs You Should Switch)
Does Your Car Need High Mileage Oil? (Signs You Should Switch) Discover More As vehicles age, their engines undergo significant wear, leading to reduced efficiency and potential breakdowns. One of the most effective ways to maintain an older engine is by switching to high-mileage oil, specially formulated for cars with 75,000 miles or more. But how do you know if your car needs it? What are the key benefits, drawbacks, and alternatives? And why should you consider Ruamnza Xrace Pro Oil for your high-mileage vehicle?

Does Your Diesel Engine Need a Special Oil? (The Truth Revealed)
Does Your Diesel Engine Need a Special Oil? (The Truth Revealed) Discover More When it comes to maintaining a diesel engine, one of the most critical decisions you’ll make is choosing the right oil. Diesel engines operate under extreme conditions—high compression, intense heat, and heavy loads—which means they require a lubricant that can withstand these challenges. But does your diesel engine really need a special oil, or can you use any high-quality motor oil? In this comprehensive guide, we’ll uncover the

What is Anti-Freeze Coolant? Types, Colors & How to Use
What is Anti-Freeze Coolant? Types, Colors & How to Use Discover More Anti-freeze coolant, also known as engine coolant or radiator fluid, is a specially formulated liquid that regulates engine temperature, prevents overheating in summer, and protects against freezing in winter. It is a mixture of water, ethylene glycol or propylene glycol, and chemical additives that enhance engine efficiency and longevity. Without proper coolant, engines can suffer from: Overheating (leading to warped cylinder heads or blown gaskets) Freezing (causing cracked engine blocks in cold climates) Corrosion (damaging radiators,
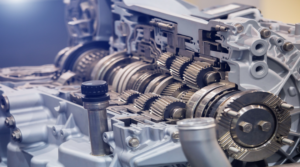
What is ATF? Types of Transmission Fluid & When to Change It
What is ATF? Types of Transmission Fluid & When to Change It Discover More Transmission fluid is one of the most critical yet often overlooked components in a vehicle’s maintenance routine. Whether you drive an automatic, manual, continuously variable transmission (CVT), or dual-clutch transmission (DCT) vehicle, the right transmission fluid ensures smooth operation, longevity, and peak performance. What is Automatic Transmission Fluid (ATF)? Automatic Transmission Fluid (ATF) is a specialized lubricant designed to reduce friction, cool transmission components, and facilitate smooth
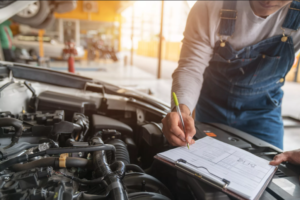
Fuel Injector Cleaner: Does It Really Work? (Analysis, Benefits, and Top Picks)
Fuel Injector Cleaner: Does It Really Work? (In-Depth Analysis, Benefits, and Top Picks) Discover More Modern engines rely on precise fuel delivery to maintain performance, efficiency, and emissions compliance. Fuel injectors play a critical role in this process by atomizing fuel into a fine mist for optimal combustion. However, over time, carbon deposits, varnish, and contaminants can clog injectors, leading to poor engine performance. Fuel injector cleaners are chemical additives designed to dissolve these deposits and restore injector efficiency. But do they
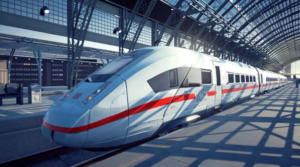
Best Railroad Engine Oils in 2025 – Boost Performance & Longevity
Best Railroad Engine Oils in 2025 – Boost Performance & Longevity Discover More The railroad industry is a backbone of global logistics, transporting millions of tons of cargo and passengers daily. Given the immense stress on locomotive engines, selecting the best railroad engine oil is crucial for optimal performance, fuel efficiency, and engine longevity. In 2025, advancements in lubrication technology have led to high-performance synthetic blends, low-ash formulations, and smart additives that enhance engine protection under extreme conditions. This guide
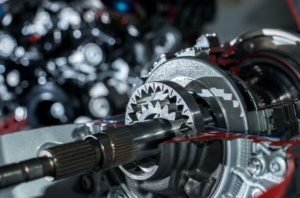
Best Transmission Treatments to Extend Your Vehicle’s Lifespan (2025 Guide)
Best Transmission Treatments to Extend Your Vehicle’s Lifespan Discover More Maintaining your vehicle’s transmission is crucial for ensuring longevity, smooth performance, and fuel efficiency. With advancements in automotive technology, transmission treatments have evolved significantly in 2025. This guide explores the best transmission treatments available, their benefits, and how they can help extend your vehicle’s lifespan. Understanding Transmission Systems and Their Importance A vehicle’s transmission is responsible for transferring power from the engine to the wheels, enabling smooth gear shifts and

What Is Xylene? Uses, Benefits & Safety Tips for Automotive & Industrial Applications
What Is Xylene? Uses, Benefits & Safety Tips for Automotive & Industrial Applications Discover More Xylene is a versatile hydrocarbon widely used in automotive, industrial, and chemical manufacturing due to its solvent properties. As a key component in paints, adhesives, and fuel additives, xylene plays a crucial role in various industrial processes. This article explores what xylene is, its primary uses, benefits in automotive and industrial applications, and essential safety tips for handling this chemical. Xylene is a colorless, flammable aromatic