A Comprehensive Guide to Mixed Hydrocarbon Oil (MHO oil)
What Is MHO Oil?
MHO full form oil is Mixed Hydrocarbon Oil (MHO) a blend of various hydrocarbon compounds, primarily consisting of alkanes, alkenes, and aromatics. These oils are obtained from crude oil through fractional distillation, and they serve as intermediate products in the petroleum industry. MHOs are versatile, as their composition varies based on the refining process and source crude oil. They are widely used in multiple industries, such as fuel, lubrication, and chemical manufacturing. The mixture can range from light to heavy hydrocarbons, making it suitable for different applications. MHO is often characterized by its density, viscosity, and boiling point range, which helps in determining its potential uses. It is considered valuable in producing various petrochemical products, and its adaptability makes it a vital component in industrial processes, contributing to both energy production and raw material supply for other sectors.
MHO Diesel Vs Diesel Oil
MHO diesel uses is a blend of various hydrocarbon fractions, often derived from refining processes, and may include recycled or lower-grade petroleum products. It is sometimes used as an alternative to standard diesel in industrial or marine applications.
Regular diesel, on the other hand, is a refined petroleum product meeting strict quality standards for use in diesel engines. It offers better combustion efficiency, lower emissions, and consistent performance compared to mho fuel.
MHO diesel is a cost-effective alternative but may not match the quality, efficiency, and regulatory compliance of regular diesel.
How is Mixed Hydrocarbon Oil (MHO) Produced?
Mixed Hydrocarbon Oil (MHO) is primarily produced through the fractional distillation of crude oil in refineries. The process begins by heating crude oil in a distillation column, where it separates into different fractions based on boiling points. Lighter hydrocarbons evaporate first, while heavier ones remain at the bottom. These fractions are then further processed through cracking, reforming, or blending to adjust the hydrocarbon composition, achieving the desired MHO properties. Cracking involves breaking down larger molecules into smaller ones, while reforming alters molecular structures to enhance fuel quality. Hydro-treating is another technique used to remove impurities like sulfur. The end result is a mixture containing alkanes, alkenes, cycloalkanes, and aromatic hydrocarbons, which are combined to form MHO. This refining process ensures that the MHO meets specific industry standards for use in various applications, such as fuels, lubricants, and feedstock for petrochemical products.
Mixed Hydrocarbon Oil Specification
Hydrocarbon mixture oil is a blend of various hydrocarbons, designed for specific industrial applications. Key specifications include:
Composition: Balanced mix of aliphatic, aromatic, and naphthenic hydrocarbons.
Density: Typically 0.75–0.95 g/cm³ (varies by blend).
Viscosity: Adjusted for application (e.g., 2–500 cSt at 40°C).
Flash Point: ≥ 60°C (ensures safety in handling).
Sulfur Content: Low (<0.1%) to minimize corrosion.
Boiling Range: Defined cut points for consistency.
Color & Odor: Clear to light yellow, mild odor (indicates purity).
Used in lubricants, solvents, and fuels, precise specs ensure performance, safety, and compliance with industry standards (e.g., ASTM, ISO).
MHO Chemical
MHO oil specification is typically consists of:
- Alkanes (Paraffins): Saturated hydrocarbons with single bonds (e.g., pentane, hexane, heptane).
- Cycloalkanes (Naphthenes): Saturated cyclic hydrocarbons that enhance lubricity (e.g., cyclopentane, cyclohexane).
- Aromatic Hydrocarbons (Arenes): Compounds with benzene rings, affecting solvency and reactivity (e.g., benzene, toluene, xylene).
Main Components of MHO
Mixed Hydrocarbon Oil (MHO) comprises a variety of hydrocarbon compounds, each contributing to its unique properties. The primary components include alkanes (saturated hydrocarbons), alkenes (unsaturated hydrocarbons with one or more double bonds), cycloalkanes (ring-structured hydrocarbons), and aromatic hydrocarbons (compounds containing benzene rings). Alkanes, such as methane, ethane, and octane, provide stability and are commonly used in fuels. Alkenes like ethylene and propylene are reactive, making them suitable for petrochemical production. Cycloalkanes add structural complexity and stability to the mixture. Aromatic hydrocarbons, including benzene, toluene, and xylene, offer high energy density and are valuable for chemical synthesis. Additionally, small amounts of sulfur, nitrogen, oxygen compounds, and trace metals may be present, depending on the source crude oil and refining process. These components collectively determine the physical and chemical characteristics, such as viscosity, boiling point, and energy content.
Key Properties of MHO
- Density: ~0.79 to 0.82 g/cm³
- Viscosity: Low, enabling smooth flow
- Boiling Range: Wide range depending on composition
- Flash Point: Typically between 40–80°C
- Energy Content: High calorific value (~45 MJ/kg)
Different Types of Mixed Hydrocarbon Oils
Mixed Hydrocarbon Oils (MHOs) vary based on their composition, boiling range, and intended applications. Common types include light, medium, and heavy MHOs.
- Light MHO: Contains a high proportion of lighter hydrocarbons like alkanes and alkenes, with lower boiling points, making it ideal for use as solvents, gasoline blending, or as feedstock in petrochemical processes.
- Medium MHO: Features a balanced mix of light and heavy hydrocarbons, with moderate boiling ranges, suitable for diesel blending, heating oils, and industrial fuel applications.
- Heavy MHO: Contains heavier, more complex hydrocarbons, often used in fuel oils, lubricants, and as raw materials for asphalt production.
Another distinction includes paraffinic, naphthenic, and aromatic MHOs, which differ in the concentration of specific hydrocarbon types. This classification helps refineries and industries choose the appropriate MHO type based on processing requirements and application needs.
Application of MHO Oil In Different Industry
Mix hydrocarbon oil uses plays a vital role across numerous industries due to its versatile nature.
- Fuel Industry: MHO serves as a blending component in gasoline, diesel, and jet fuel, enhancing fuel properties like energy density and combustion efficiency.
- Chemical Industry: It acts as a feedstock for producing various petrochemicals, such as ethylene, propylene, and benzene, which are building blocks for plastics, synthetic fibers, and rubbers.
- Lubricant Production: MHO is processed into lubricating oils used in engines, machinery, and industrial equipment, ensuring smooth operation and reducing wear.
- Solvent Manufacturing: Light MHOs are employed as solvents in paint, coatings, and adhesives.
- Asphalt and Bitumen Production: Heavy MHOs are essential in creating asphalt for road construction and roofing materials.
Its adaptability makes MHO indispensable in multiple sectors, contributing to everyday products and industrial processes.
MHO Oil Uses & MHO petroleum products
Also mixed hydrocarbon oil uses is versatile petroleum-based product used across various industries due to its unique composition of alkanes, cycloalkanes, and aromatics. Here are some of its primary applications:
1. Fuel Industry
- Used as a blending component in diesel, gasoline, and jet fuel to enhance combustion properties.
- Acts as an alternative fuel source in industrial burners and boilers for power generation.
2. Lubricants and Greases
- Serves as a base oil in the production of industrial lubricants and greases, reducing friction in machinery.
- Used in metalworking fluids for cooling and lubrication during machining processes.
3. Chemical and Petrochemical Industry
- A crucial feedstock for petrochemical production, including ethylene, benzene, and toluene, used in plastics, rubber, and synthetic fibers.
- Used in paint, coatings, and adhesives as a solvent.
4. Solvent and Cleaning Agents
- Functions as an industrial solvent in degreasing agents and cleaning solutions.
- Helps dissolve oils, greases, and other organic compounds in manufacturing and maintenance processes.
5. Textile Industry
- Used as a carrier fluid in textile dyeing and printing processes.
- Helps in achieving uniform coloration of fabrics.
6. Metal and Machinery Industry
- Serves as a cooling and lubricating agent in metal cutting, forming, and processing.
- Used in corrosion prevention coatings for industrial equipment.
7. Power Generation
- Used as a fuel in power plants for steam generation and electricity production.
- Provides efficient energy output when used in industrial burners and furnaces.
8. Rubber and Plastic Manufacturing
- Acts as a softening and processing aid in rubber and plastic manufacturing.
- Improves the flexibility and durability of rubber-based products.
9. Automotive Industry
- Found in engine oils and fuel additives to enhance engine performance.
- Used in undercoating and rust prevention applications.
Uses of MHO Diesel
Mixed Hydrocarbon Oil (MHO) Diesel is a fuel alternative widely used in various industrial and commercial applications:
- Industrial Fuel: Used in boilers, furnaces, and power plants for efficient energy generation.
- Blending Component: Mixed with diesel fuels to improve combustion efficiency and reduce costs.
- Heavy Machinery & Equipment: Powers construction, mining, and agricultural machinery.
- Backup Generators: Used in standby power generators for uninterrupted electricity supply.
- Marine Fuel: Suitable for boats, ships, and marine engines as an economical fuel option.
- Heating Applications: Used in industrial heating systems and kilns.
MHO diesel is a cost-effective fuel alternative, providing energy efficiency for industrial and commercial applications.
How is the Quality of MHO Assessed
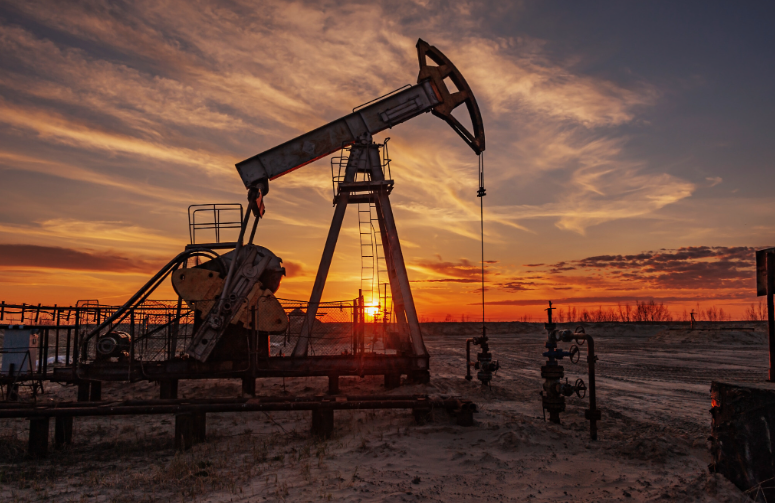
The quality of Mixed Hydrocarbon Oil (MHO) is assessed through various testing methods to ensure it meets industry standards and requirements. Common parameters evaluated include density, viscosity, boiling point range, flash point, and pour point. Density and viscosity indicate the oil’s fluidity and behavior under different temperatures. Boiling point range helps determine the suitability of MHO for specific applications, such as fuel blending or lubricant production. Flash point and pour point tests reveal safety and performance characteristics, particularly under extreme conditions. Additionally, chemical composition analysis using gas chromatography and mass spectrometry identifies the types and concentrations of hydrocarbons present. The presence of impurities like sulfur, nitrogen, oxygen, and trace metals is also checked, as they can affect performance and environmental compliance. These tests help refineries and industries maintain consistent MHO quality, ensuring its effective use in various applications.
Benefits of MHO oil
Mixed Hydrocarbon Oil (MHO) offers several benefits, making it valuable across multiple industries. Its versatility allows it to serve as a raw material for producing fuels, lubricants, and petrochemicals. As a fuel blending component, MHO enhances combustion efficiency and energy output, contributing to improved fuel performance. In the chemical industry, it provides an essential feedstock for manufacturing plastics, resins, and synthetic fibers. MHO’s adaptability in lubrication helps reduce friction, wear, and tear in machinery, extending equipment lifespan. Additionally, its wide availability and cost-effectiveness make it a practical choice for industrial applications. The ability to customize MHO properties through refining and blending processes further enhances its value, enabling tailored solutions for specific needs. These benefits make MHO a crucial asset in the energy, manufacturing, and transportation sectors.
Environmental Impacts of MHO
Mixed Hydrocarbon Oil (MHO) can have significant environmental impacts if not managed properly. During extraction, refining, and transportation, accidental spills can lead to soil and water contamination, harming aquatic and terrestrial ecosystems. The burning of MHO-based fuels releases greenhouse gases such as CO₂, contributing to climate change and air pollution. Additionally, incomplete combustion produces pollutants like carbon monoxide (CO), sulfur oxides (SOx), nitrogen oxides (NOx), and particulate matter, which pose health risks. Improper disposal of MHO residues can contaminate land and groundwater, affecting plant and animal life. Efforts to mitigate these impacts include using cleaner refining technologies, implementing spill prevention measures, and adopting stricter emission controls. Shifting towards more sustainable energy sources can also reduce the reliance on MHO, minimizing its environmental footprint.
MHO Stored and Transported Safely
Storing and transporting Mixed Hydrocarbon Oil (MHO) requires strict safety measures to prevent accidents, spills, and contamination. MHO is typically stored in metal tanks or drums designed to withstand pressure and temperature variations. These storage facilities must have proper ventilation to prevent vapor accumulation and minimize fire hazards. Anti-static precautions are essential to prevent sparks that could ignite vapors. During transportation, MHO is carried in tanker trucks, railcars, or ships equipped with safety features such as pressure relief valves and leak detection systems. Regular inspections ensure the integrity of tanks and transportation vehicles. Proper labeling, handling guidelines, and emergency response plans are crucial to minimize risks. Workers involved in storage and transportation must follow safety protocols, wear protective gear, and be trained to handle potential incidents.
How Does MHO Differ from Other Hydrocarbon Oils
Mixed Hydrocarbon Oil (MHO) differs from other hydrocarbon oils in terms of composition, application, and production process. While MHO is a blend of various hydrocarbons like alkanes, alkenes, cycloalkanes, and aromatics, other oils might be more uniform in composition. For example, mineral oils primarily consist of alkanes and are used in lubricants and cosmetics. In contrast, MHO is more versatile, serving multiple purposes, including fuel blending, lubrication, and chemical feedstock. Unlike crude oil, which is a raw, unrefined mixture, MHO undergoes specific refining processes to achieve desired properties. Additionally, MHO’s adaptability allows it to be tailored for various applications, making it more flexible compared to single-component oils like kerosene or diesel.
Common Additives Used in MHO
Additives are often used in Mixed Hydrocarbon Oil (MHO) to enhance its properties and performance. Antioxidants are added to prevent oxidation, prolonging shelf life and reducing sludge formation. Corrosion inhibitors protect storage tanks and pipelines from rust. Pour point depressants improve flow properties in colder temperatures, while viscosity improvers ensure consistent performance across temperature variations. Anti-foaming agents prevent foam formation during processing and handling. Detergents and dispersants keep engines clean by preventing the buildup of deposits and sludge. These additives ensure that MHO meets industry requirements, performs efficiently, and remains stable during storage and transportation.
How is MHO Refined or Processed
Refining Mixed Hydrocarbon Oil (MHO) involves several processes to enhance its properties for industrial applications. These include fractional distillation, cracking, and reforming, which separate hydrocarbons based on boiling points and break down larger molecules. Hydrotreating removes impurities like sulfur and nitrogen, ensuring the final product meets quality standards. Further processing, such as blending, adjusts the composition to achieve desired characteristics. This refining ensures that MHO is suitable for use as fuel, lubricants, or petrochemical feedstock.
How Does MHO Affect Engine Performance
MHO contributes to smoother engine operation by providing adequate lubrication, improving fuel efficiency, and reducing wear and tear. Its balanced composition ensures consistent combustion and performance in engines.
Methods for Testing MHO Purity
Final Thoughts
FAQs
Hydrocarbon oil is a liquid derived from crude oil, consisting mainly of hydrocarbons. It includes various petroleum-based oils such as mineral oil, lubricating oil, and fuel oil, used in engines, industrial applications, and as a chemical feedstock.
An MHO relay is a distance protection relay that detects faults by measuring line impedance, with a trip zone shaped like a circle in the impedance plane. The offset MHO relay shifts this circle into the third quadrant, improving sensitivity for nearby faults (including reverse-direction faults). This makes it useful for protecting transformers and busbars. Both relays help secure power lines against short circuits.
Mixed Hydrocarbon Oil (MHO) is used as an alternative fuel, industrial solvent, and blending component in petroleum products. It is commonly used in power plants, marine applications, and industrial heating systems.
Mixed mineral hydrocarbon oil is a blend of refined mineral oils used for lubrication in industrial and automotive applications. It combines different base oils and additives to enhance properties like viscosity, lubricity, and thermal stability.
Unlike crude oil, which is unrefined, MHO undergoes refining processes to achieve specific properties suitable for industrial applications.
MHO is widely used in the fuel, chemical, automotive, and manufacturing industries.
Yes, MHO is highly flammable and should be handled with proper safety measures to prevent accidents.
MHO is usually blended with other fuels to improve combustion efficiency but is not typically used directly as a standalone fuel.
Yes, improper handling and combustion of MHO can cause soil, water pollution, and air emissions, contributing to environmental concerns.
An oily mixture of hydrocarbons refers to a blend of different hydrocarbon compounds, typically found in crude oil, lubricants, or fuel blends. These mixtures vary in viscosity and composition and are used in energy production, lubrication, and chemical processing.
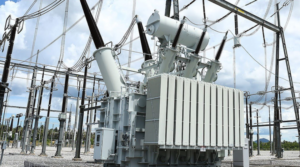
What is Transformer Oil? Types, Properties & Uses Explained
What is Transformer Oil? Types, Properties, Uses, and Comparisons Discover More Transformer oil is a critical component in electrical power systems, ensuring the efficient and safe operation of transformers. It acts as both an insulator and a coolant, preventing electrical breakdowns and dissipating heat generated during transformer operation. In this detailed guide, we will explore what transformer oil is, its different types, key properties, applications, maintenance, and how to choose the best oil for your needs. We’ll also introduce Rumanza

Does Your Car Need High Mileage Oil? (Signs You Should Switch)
Does Your Car Need High Mileage Oil? (Signs You Should Switch) Discover More As vehicles age, their engines undergo significant wear, leading to reduced efficiency and potential breakdowns. One of the most effective ways to maintain an older engine is by switching to high-mileage oil, specially formulated for cars with 75,000 miles or more. But how do you know if your car needs it? What are the key benefits, drawbacks, and alternatives? And why should you consider Ruamnza Xrace Pro Oil for your high-mileage vehicle?

Does Your Diesel Engine Need a Special Oil? (The Truth Revealed)
Does Your Diesel Engine Need a Special Oil? (The Truth Revealed) Discover More When it comes to maintaining a diesel engine, one of the most critical decisions you’ll make is choosing the right oil. Diesel engines operate under extreme conditions—high compression, intense heat, and heavy loads—which means they require a lubricant that can withstand these challenges. But does your diesel engine really need a special oil, or can you use any high-quality motor oil? In this comprehensive guide, we’ll uncover the

What is Anti-Freeze Coolant? Types, Colors & How to Use
What is Anti-Freeze Coolant? Types, Colors & How to Use Discover More Anti-freeze coolant, also known as engine coolant or radiator fluid, is a specially formulated liquid that regulates engine temperature, prevents overheating in summer, and protects against freezing in winter. It is a mixture of water, ethylene glycol or propylene glycol, and chemical additives that enhance engine efficiency and longevity. Without proper coolant, engines can suffer from: Overheating (leading to warped cylinder heads or blown gaskets) Freezing (causing cracked engine blocks in cold climates) Corrosion (damaging radiators,
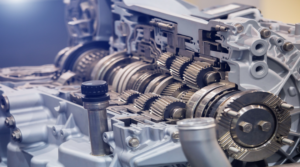
What is ATF? Types of Transmission Fluid & When to Change It
What is ATF? Types of Transmission Fluid & When to Change It Discover More Transmission fluid is one of the most critical yet often overlooked components in a vehicle’s maintenance routine. Whether you drive an automatic, manual, continuously variable transmission (CVT), or dual-clutch transmission (DCT) vehicle, the right transmission fluid ensures smooth operation, longevity, and peak performance. What is Automatic Transmission Fluid (ATF)? Automatic Transmission Fluid (ATF) is a specialized lubricant designed to reduce friction, cool transmission components, and facilitate smooth
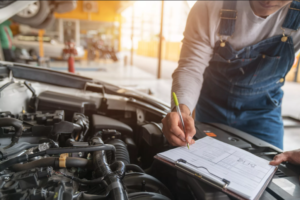
Fuel Injector Cleaner: Does It Really Work? (Analysis, Benefits, and Top Picks)
Fuel Injector Cleaner: Does It Really Work? (In-Depth Analysis, Benefits, and Top Picks) Discover More Modern engines rely on precise fuel delivery to maintain performance, efficiency, and emissions compliance. Fuel injectors play a critical role in this process by atomizing fuel into a fine mist for optimal combustion. However, over time, carbon deposits, varnish, and contaminants can clog injectors, leading to poor engine performance. Fuel injector cleaners are chemical additives designed to dissolve these deposits and restore injector efficiency. But do they
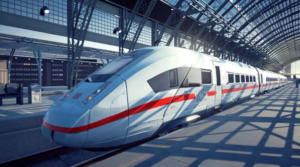
Best Railroad Engine Oils in 2025 – Boost Performance & Longevity
Best Railroad Engine Oils in 2025 – Boost Performance & Longevity Discover More The railroad industry is a backbone of global logistics, transporting millions of tons of cargo and passengers daily. Given the immense stress on locomotive engines, selecting the best railroad engine oil is crucial for optimal performance, fuel efficiency, and engine longevity. In 2025, advancements in lubrication technology have led to high-performance synthetic blends, low-ash formulations, and smart additives that enhance engine protection under extreme conditions. This guide
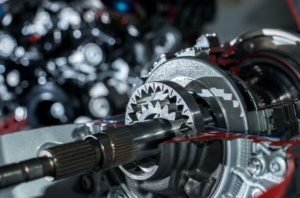
Best Transmission Treatments to Extend Your Vehicle’s Lifespan (2025 Guide)
Best Transmission Treatments to Extend Your Vehicle’s Lifespan Discover More Maintaining your vehicle’s transmission is crucial for ensuring longevity, smooth performance, and fuel efficiency. With advancements in automotive technology, transmission treatments have evolved significantly in 2025. This guide explores the best transmission treatments available, their benefits, and how they can help extend your vehicle’s lifespan. Understanding Transmission Systems and Their Importance A vehicle’s transmission is responsible for transferring power from the engine to the wheels, enabling smooth gear shifts and

What Is Xylene? Uses, Benefits & Safety Tips for Automotive & Industrial Applications
What Is Xylene? Uses, Benefits & Safety Tips for Automotive & Industrial Applications Discover More Xylene is a versatile hydrocarbon widely used in automotive, industrial, and chemical manufacturing due to its solvent properties. As a key component in paints, adhesives, and fuel additives, xylene plays a crucial role in various industrial processes. This article explores what xylene is, its primary uses, benefits in automotive and industrial applications, and essential safety tips for handling this chemical. Xylene is a colorless, flammable aromatic

Best Automotive Grease for High-Temp Performance (Buyer’s Guide)
Best Rumanza Automotive Grease for High-Temp Performance (Buyer’s Guide) Discover More Automotive grease is a crucial component in vehicle maintenance, ensuring smooth operation and longevity of mechanical parts. Among the various brands available, Rumanza automotive grease has emerged as a top choice for high-temperature performance, offering superior lubrication under extreme conditions. Whether you’re maintaining a passenger car, heavy-duty truck, or industrial machinery, selecting the right grease can significantly impact performance, fuel efficiency, and component lifespan. This comprehensive buyer’s guide explores the best Rumanza grease products designed for

Fuel System Cleaner: How It Works & Why Your Car Needs It
Fuel System Cleaner: How It Works & Why Your Car Needs It Discover More Modern vehicles rely on highly efficient fuel systems to deliver optimal performance, fuel economy, and reduced emissions. However, over time, carbon deposits, varnish, and other contaminants accumulate in critical components such as fuel injectors, intake valves, and combustion chambers. These deposits can lead to poor engine performance, reduced fuel efficiency, and increased emissions. Rumanza Fuel System Cleaner is a premium fuel additive designed to deep-clean, protect, and enhance your vehicle’s

Liquefied Natural Gas (LNG): Benefits, Uses & Why You Should Switch Today
Liquefied Natural Gas (LNG): Benefits, Uses & Why You Should Switch Today Discover More The global energy sector is undergoing a significant transformation, driven by the urgent need for cleaner, more efficient, and sustainable fuel alternatives. Among the most promising solutions is Liquefied Natural Gas (LNG), which offers a compelling combination of environmental benefits, cost efficiency, and versatility. As nations and industries strive to meet climate goals and reduce reliance on traditional fossil fuels, LNG has emerged as a key transitional energy source that bridges the